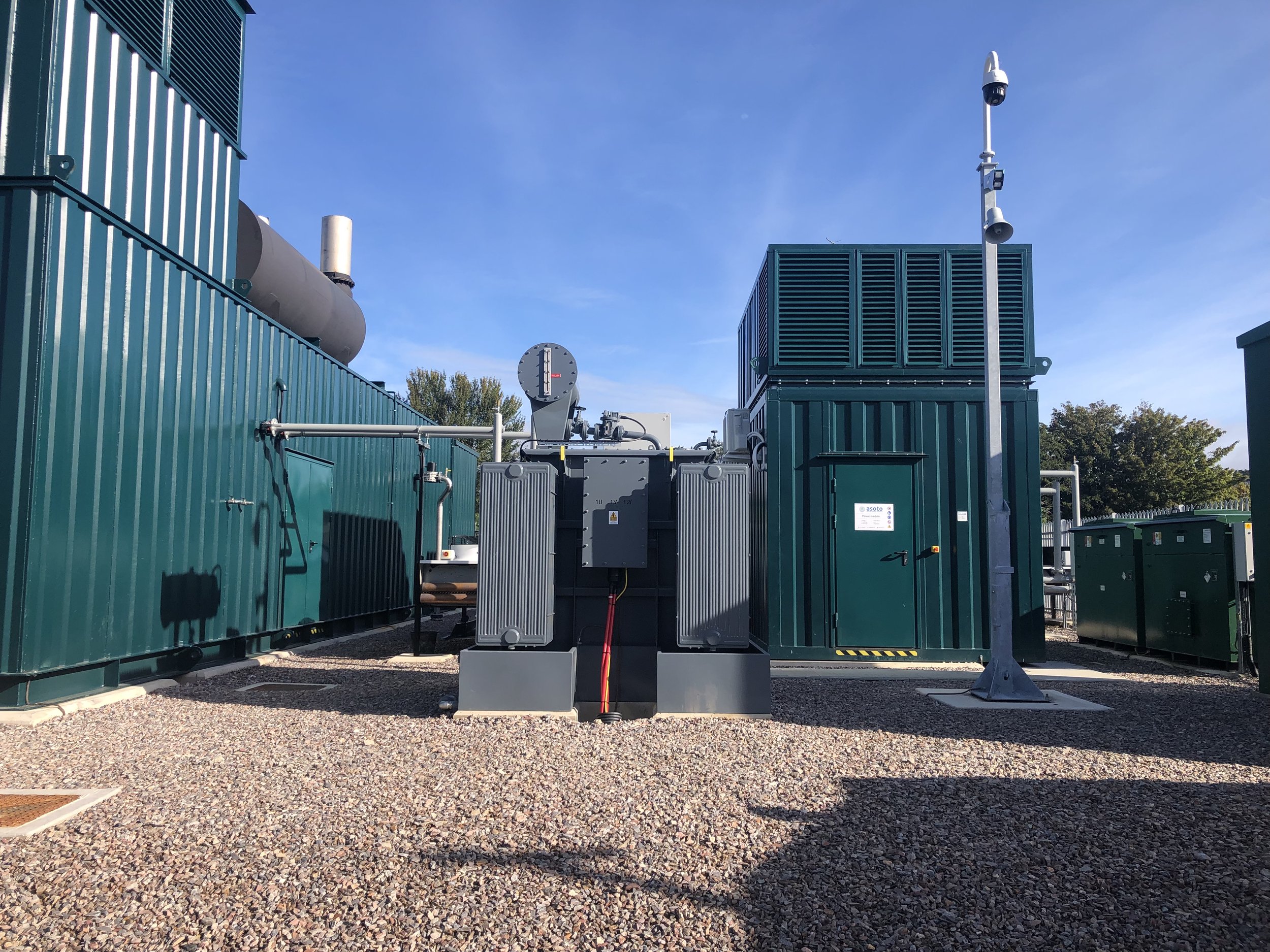
Containerized, plug&play power modules - Plymouth, UK
We delivered two Power modules for the Power Plant in Plymouth, UK. One of the modules is equipped with a Jenbacher J620 3MW engine, and the other has an MTU V20 4000 L63 2MW engine. The power plant stabilizes the local electricity grid. Our team commissioned the modules, and we also provide ongoing technical support and necessary maintenance and servicing of the Power modules.
Both of these engines are overhauled. During the overhaul, the engine is disassembled and inspected for wear or damage, and any damaged or worn parts are replaced. Next, the engine is reassembled and tested to ensure it meets the same standards as a brand-new engine. An overhauled engine is a reliable and cost-efficient alternative to a brand-new one.
These power modules run on natural gas, a relatively clean-burning fuel that can be highly efficient in generating electricity. As a result, the power modules can achieve high levels of efficiency, resulting in lower operating costs and reduced greenhouse gas emissions.
The plug&ply power modules come in transportable and spacious steel containers divided into the machine room and the control room. The machine room accommodates the genset and all necessary auxiliaries, while the control room houses safety and control systems.
The dimensions for the containerized power plant, with exhaust and cooling systems mounted, are 17,230 x 5,225* x 6,602* This is because the highest point of the exhaust pipe end is 6,602*mm.
Asoto built these containerized power modules to operate at an ambient temperature from -10oC to+30oC, and the minimum noise requirement being 55dB(A)at 10m.
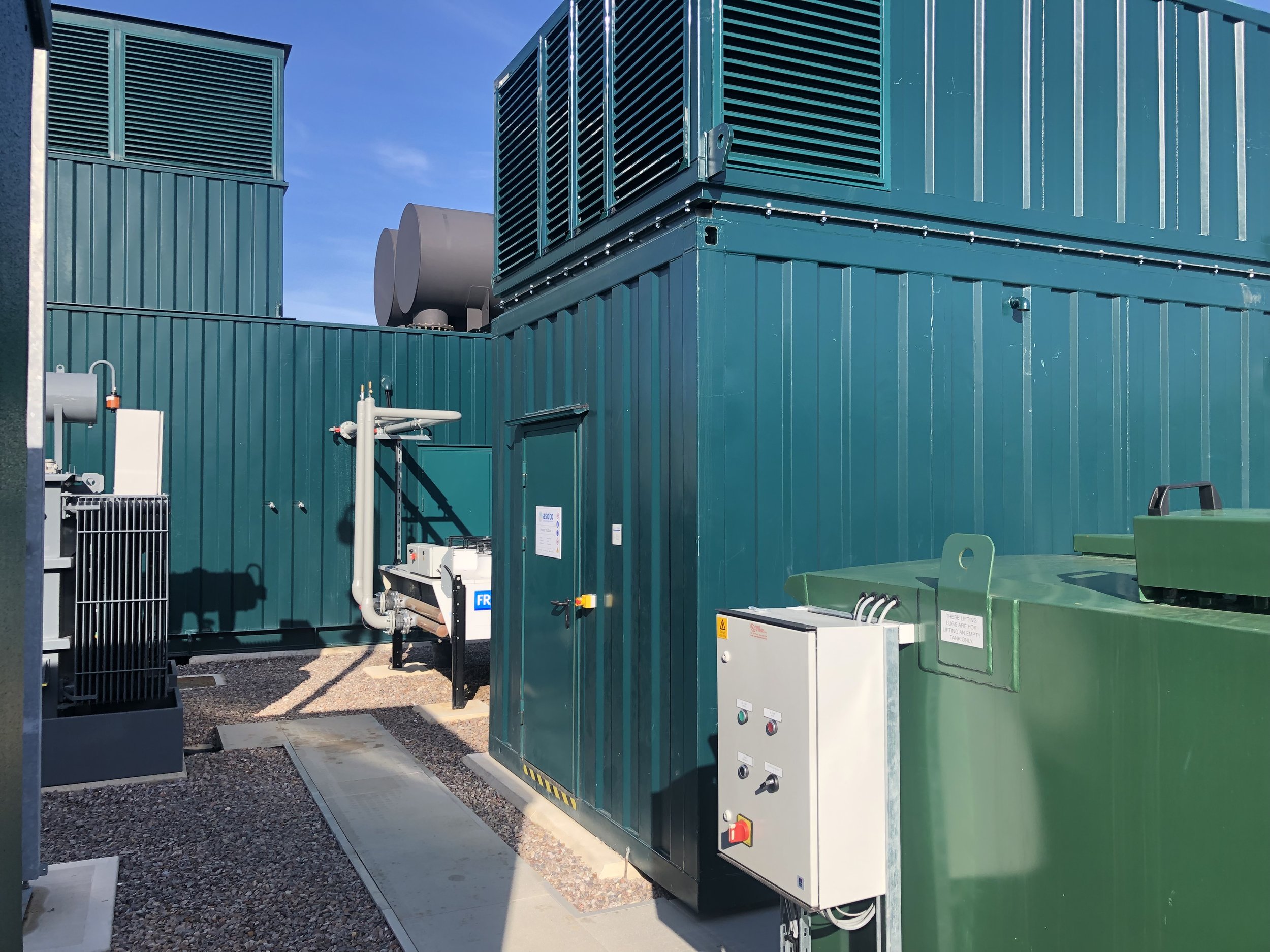
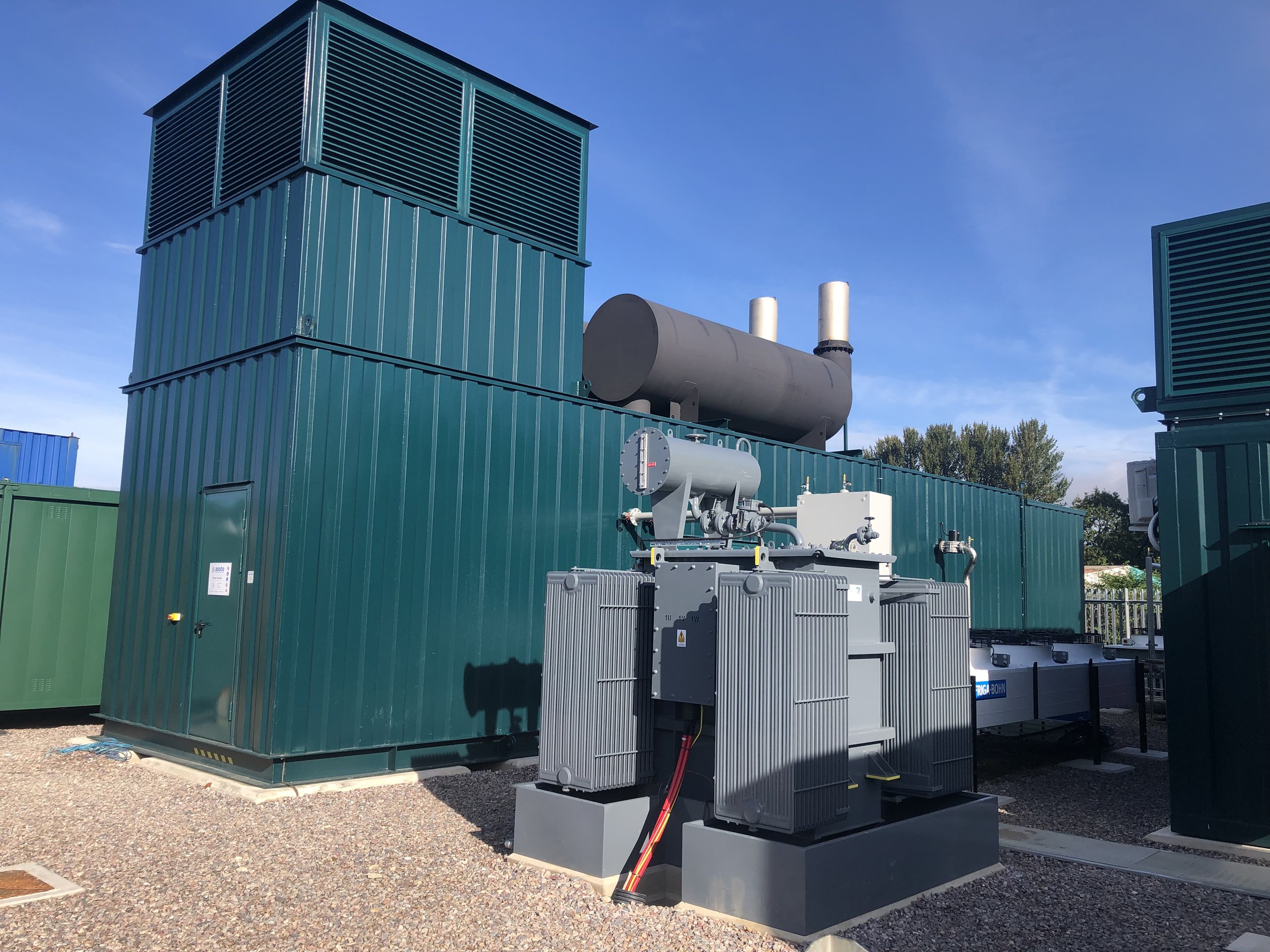
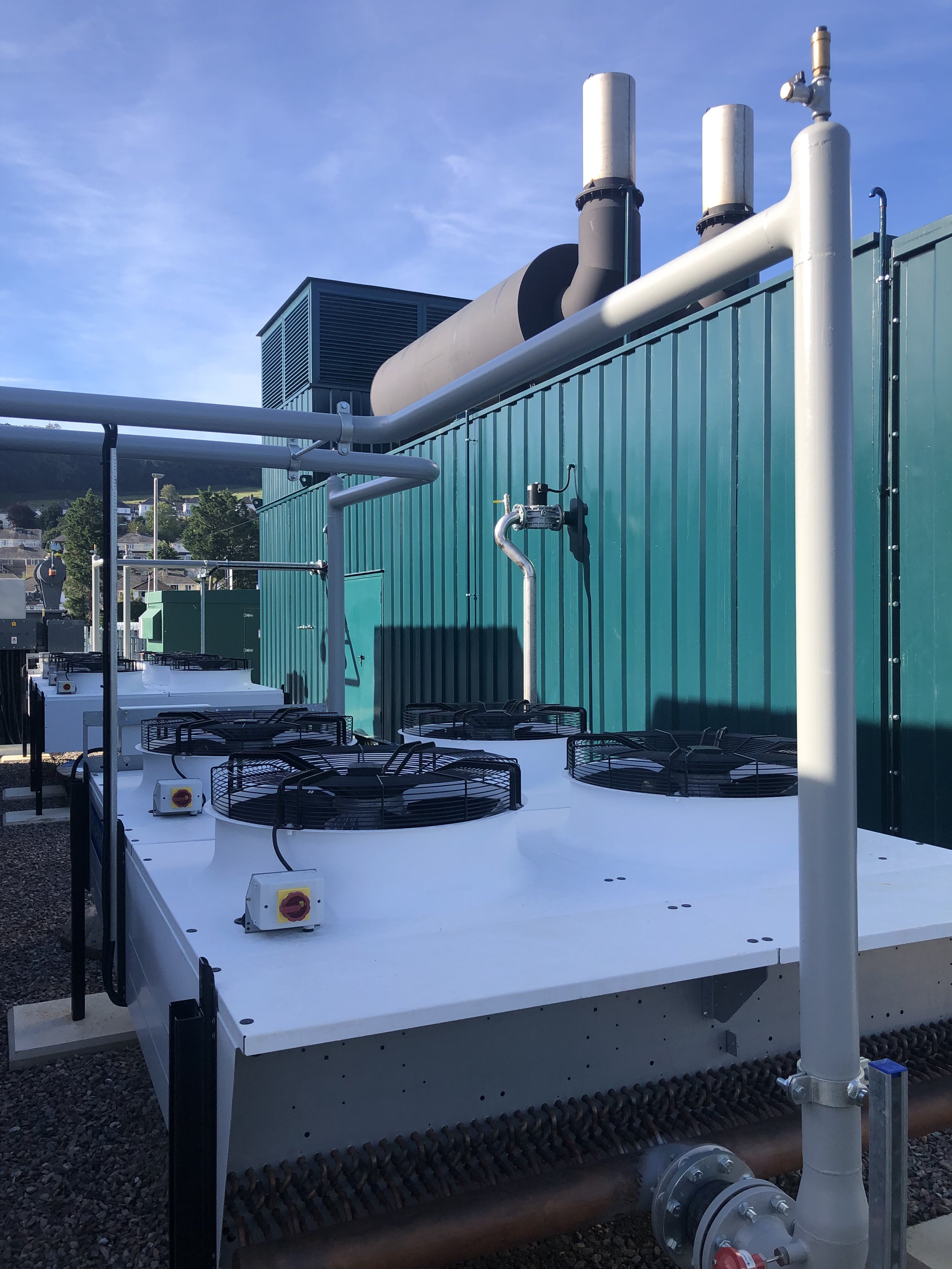
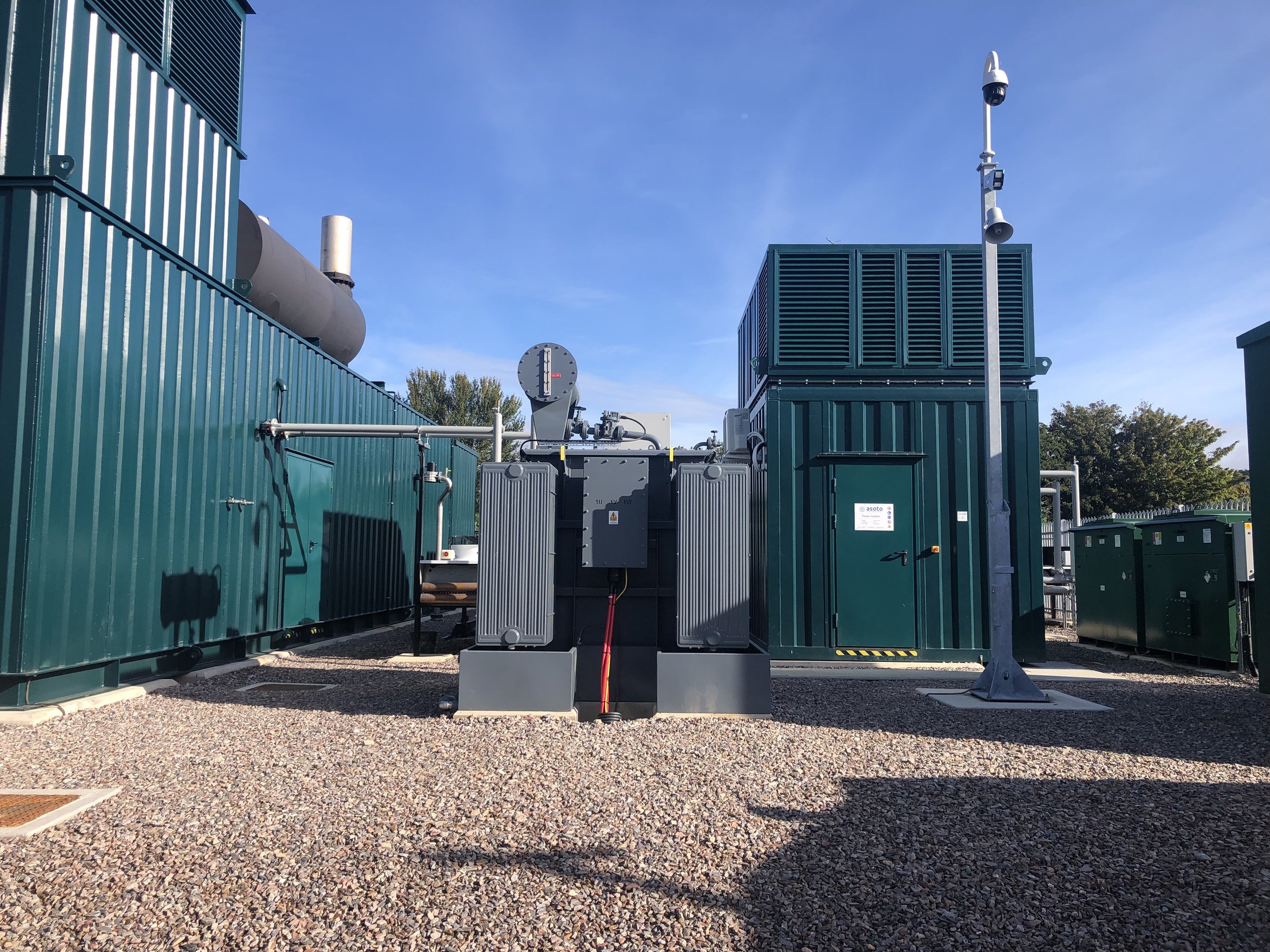
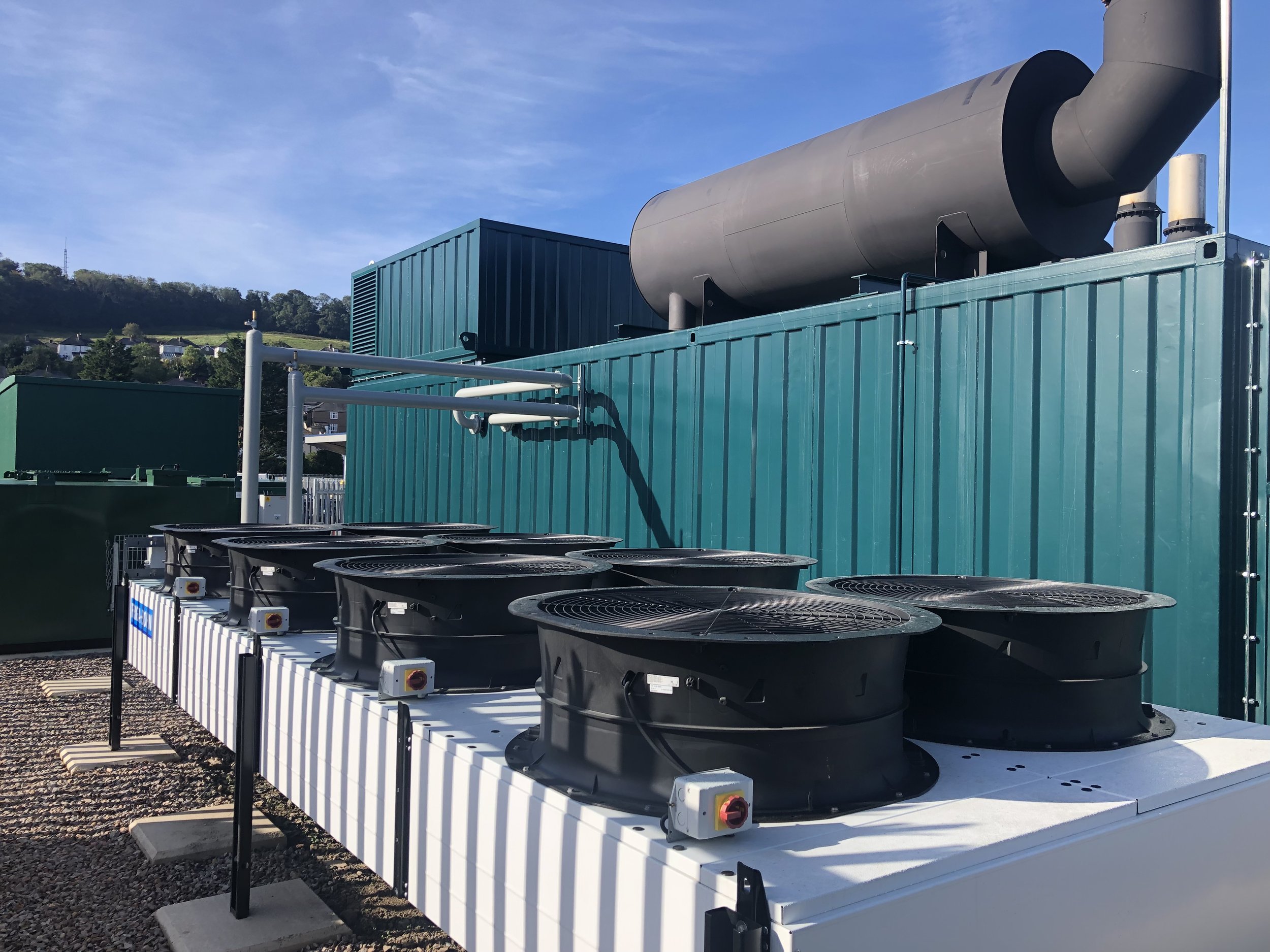
The Layout:
External:
Exhaust Gas Silencer
A free-standing silencer with integrated catalytic converter elements. The engine’s frequency band, the required target levels, and the possible pressure drop are considered to reduce sound emissions.
Dry Cooler
Customized, horizontal design flat coolers to meet the engine requirements, ambient temperature, and noise restrictions. As for the power plant specification, the dry coolers are placed on the ground beside the containers.
Access ladder to roof and railing
Steel ladder and railings to provide access and safety during maintenance work and checkups of auxiliary equipment.
Gas connection flance
Connection point to the plant's gas line.
Internal:
Generator Set
Jenbacher J620 3MW engine, and an MTU V20 4000 L63 2MW.
Air inlet silencer
Series of sound-absorbing panels designed to limit the noise generated by the power module and allow an optimal flow of the combustion air in the engine room.
Air outlet silencer
Sound-absorbing panels are positioned to limit the noise generated by the power module and allow steady exhaust airflow..
Air supply fans
Engine room ventilation to ensure the discharging of the radiant heat from the unit and for combustion air supply to the engine.
Engine heating system
The engine heating system warms up the engine and keeps it at a ready-to-start temperature, ensuring faster engine starts and reducing engine wear.
Engine cooling system
The engine cooling system removes excess heat to maintain the engine operating temperature so it can work most efficiently.
Gas train
The gas train supplies the engine with gas and contains regulatory, measurement, and control elements.
Oil tanks
A tank for the storage of lubricating oil is installed in the container.
Control systems and panels
A user-friendly engine management system that provides engine management, monitoring, and control. All error messages are date stamped to identify the sequence of events.
Safety systems and equipment
Smoke alarm system with detectors in the machine and control room and a gas warning device in the machine room. Powder fire extinguisher in the control room
Air temperature control system
Air temperature sensor in the machine room. Heating radiator in the machine room. Electric heating/cooling in the control room as well
Here are some of the projects we've delivered to our clients.
-
Sittingbourne, UK.
Flexible generation power plant to balance the local electricity network and ensure grid resiliency.
3 containerized power modules with a combined power of 8.1MW
-
Lowestoft, UK.
Fueled by natural gas, the power module is dedicated to the production of electrical energy.
Containerized power module with a power output of 3MW.
-
Yeovil, UK.
Flexible generation power plant to ensure fast response, secure and flexible generation to ensure grid resiliency.
2 containerized power modules with a combined power of 5.4 MW.